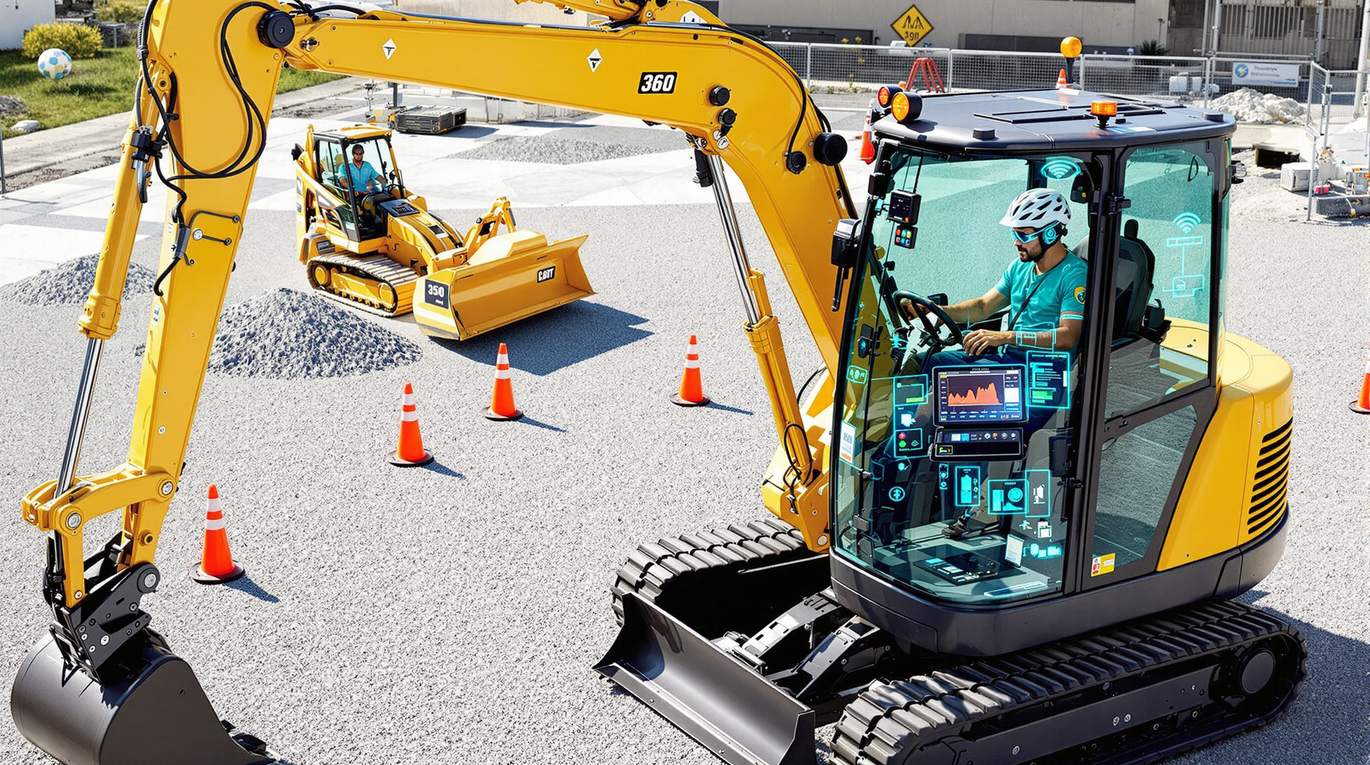
Construction equipment theft costs businesses up to $1 billion annually. This makes state-of-the-art safety products more significant than ever to protect valuable machinery investments. The industry has seen remarkable advancements in equipment security and operator safety, from 360-degree visibility systems to AI-powered monitoring solutions.
Modern safety innovations are nowhere near simple anti-theft measures. Smart operator authentication, fatigue detection systems, and up-to-the-minute monitoring capabilities now enhance compact equipment's technology. These features can reshape your equipment's safety profile for 2025 and beyond.
Let's break down the must-have safety features for your compact machinery. We'll get into AI-powered solutions and share practical implementation strategies that make sense for your business.
Essential Safety Features for Modern Compact Equipment
Modern compact machinery just needs strong safety measures to protect operators and equipment. In 2025, telematics has become the life-blood technology that helps companies prevent equipment theft and monitor machine usage with incredible precision.
Automated emergency shutdown systems
Advanced emergency shutdown systems now come with sophisticated fail-safe mechanisms that stop operations instantly when they detect hazardous conditions. These systems employ multiple-point disconnects and automated shutdown algorithms to respond quickly during critical situations. On top of that, modern shutdown systems use digital sensors to review process variables continuously and respond automatically when safety limits are exceeded.
Smart operator authentication
Operator authentication plays a crucial role in manufacturing safety and security. Radio-frequency identification (RFID) technology tracks operator activities precisely and enhances workforce management. Each operator gets unique identification codes to ensure only certified personnel can access specific equipment, which reduces unauthorized usage risks.
Real-time load monitoring
Load monitoring capabilities have improved substantially and provide precise measurements in operating conditions of all types. Modern systems deliver accurate immediate monitoring of load-bearing connections, with standard capacities from 2 to 2000 tons. These systems collect machine data 24/7/365 to monitor equipment performance.
The integration of these safety features has reshaped how companies handle equipment security. Manufacturers focus heavily on operator comfort and safety by introducing pressurized sealed cabs that reduce noise levels and create safer work environments. Rearview cameras have become standard equipment to help operators stay aware of their surroundings constantly.
These safety technology advances line up with the growing need for compact equipment in urban construction projects. Space constraints and precision requirements make safety innovations vital. Jonathan Gardner, Product Manager for Construction Equipment at Kubota Canada, points out that companies see the benefits of compact equipment in industries of all types, from landscape and construction to snow removal operations.
AI-Powered Safety Innovations
AI-powered safety features revolutionized compact equipment operations in 2025. These breakthrough safety products blend advanced sensors with intelligent algorithms that create safer work environments.
Predictive maintenance alerts
Smart algorithms analyze equipment data to detect problems before breakdowns occur. Research shows AI-powered predictive maintenance reduces machine downtime by 20% to 40%. These systems use sensors to monitor critical components and provide early warnings about equipment's health.
VIA Safety Solution demonstrates this breakthrough with its precise monitoring capabilities. The system tracks vehicle performance metrics and sends alerts immediately after detecting irregularities. Maintenance teams can fix problems before they become serious rather than after they occur.
Operator fatigue detection
Sophisticated operator monitoring systems represent remarkable safety breakthroughs. Modern compact equipment includes non-intrusive, in-cab detection technology that alerts operators as soon as it spots fatigue.
The technology measures geometric features of the face to detect mental fatigue in construction equipment operators. These systems look at:
- Eye movement patterns
- Head position changes
- Facial expressions
VIA's Driver Safety System advances this technology by spotting early signs of stress and fatigue. The system tells operators when to take breaks and encourages safe driving practices. This approach prevents accidents that operator exhaustion might cause.
These systems analyze data immediately to warn about safety risks before they become dangerous. The technology spots subtle factors like chronic stress, anxiety, and isolation that affect operator judgment.
Research shows driver drowsiness causes 21% of fatal crashes. Companies like Caterpillar and Hexagon built these safety features into their equipment, which improved workplace safety significantly. Major mining companies that use Caterpillar's autonomous systems report zero workplace injuries since they started using them.
Smart Connectivity Features
Smart connectivity has changed how companies track and manage their compact equipment fleets. Companies now use immediate data through advanced IoT integration to improve operational safety and efficiency at multiple worksites.
Remote monitoring capabilities
Modern remote monitoring systems give detailed oversight of equipment performance and operator behavior. These systems gather vital data through sensors that provide instant visibility into operational movements and make field workforce safer. Supervisors can now check data from wearable devices and condition-monitoring sensors to spot problems like temperature spikes or unsafe work behavior.
Remote monitoring has shown impressive results. Studies reveal a 25-30% reduction in downtime incidents and a 10-15% improvement in asset use. On top of that, IoT-enabled sensors monitor environmental conditions to maintain worksite safety and regulatory compliance.
Fleet management integration
Modern fleet management platforms combine data from multiple sources to provide applicable information. These systems keep track of equipment location, usage patterns, and maintenance schedules while sending immediate alerts about potential safety risks.
Smart telematics solutions make maintenance schedules better and cut fuel consumption by monitoring equipment performance precisely. These systems have proven valuable as organizations report up to a 40% reduction in accidents and injuries at multiple sites.
Data analytics for safety
Advanced analytics platforms turn collected data into meaningful safety insights. These systems process information from various sources, including:
- Equipment performance metrics
- Operator behavior patterns
- Environmental conditions
- Maintenance records
Organizations can find why safety incidents happen by analyzing sensor data, digital work records, and safety checklist accuracy through detailed data analysis. This approach helps companies determine if safety incidents come from machinery defects, incorrect work procedures, or operator fatigue.
Data-driven safety management makes a big difference. Innovative safety products show a 15% decrease in work-related illnesses through better environmental sensing and analysis. Companies can then develop specific safety protocols to stop similar incidents from happening again.
Implementing New Safety Technology
Safety products need smart implementation that takes into account both money matters and how ready workers are to use them. Recent studies show that organizations don't deal very well with adopting new safety tech, but good planning makes these challenges easier to handle.
Cost considerations
Businesses see the upfront cost as their biggest problem when rolling out new safety technology. The purchase costs have dropped over the last several years, but companies need to weigh the long-term benefits against immediate expenses. Construction sites offer a clear example - a typical strain injury costs about $50,000, while a slip and fall accident can run up to $94,000.
Companies should take these steps to get the most from their tech investments:
- Look at how reduced accidents affect return on investment
- Add lifecycle costs to the purchase price
- Check what it costs to work with existing systems
- Include training and maintenance costs
A soaring 83% of workers say they're ready to try new safety tech at work. This shows strong worker backing for safety investments, even with cost worries.
Training requirements
Training programs are a vital part of successful tech adoption. About 76% of employers call lack of proper training their main concern. Organizations need training strategies that cover:
Equipment operation and maintenance are everything in safety training. Studies show 42% of workers blame workplace injuries on poor training. This makes ongoing education and skill building a top priority.
Worker challenges often come from job security fears and finding skilled staff. A user-friendly interface and regular training sessions help solve these issues. Numbers show that companies with complete training programs see 21% more profit.
Organizations must see that new tech needs both system integration and culture change. About 48% of employers think their current safety gear works well. This highlights why companies need to show clear benefits through solid training and support when bringing in new technology.
Conclusion
Safety technology in compact machinery has evolved substantially. Equipment protection and operator safety are now more reliable than ever before. AI-powered fatigue detection and smart authentication systems create multiple protective layers that safeguard valuable assets.
Real-life data shows these safety innovations work exceptionally well. Companies with complete safety solutions report up to 40% fewer accidents. Their predictive maintenance systems also reduce downtime by 20-40%. These results show clear advantages beyond simple security measures.
The original costs may look high, but modern safety features' long-term benefits exceed the investment. Companies see measurable returns through lower accident rates, better operator performance, and improved equipment lifespan. Smart connectivity lets managers monitor entire fleets precisely. Data analytics help them prevent potential incidents before they happen.
New safety technology's success largely depends on proper implementation and training. Companies that make complete training programs a priority achieve better adoption rates and stronger safety outcomes. The technology keeps advancing, and staying current with safety innovations helps protect both equipment and operators effectively.