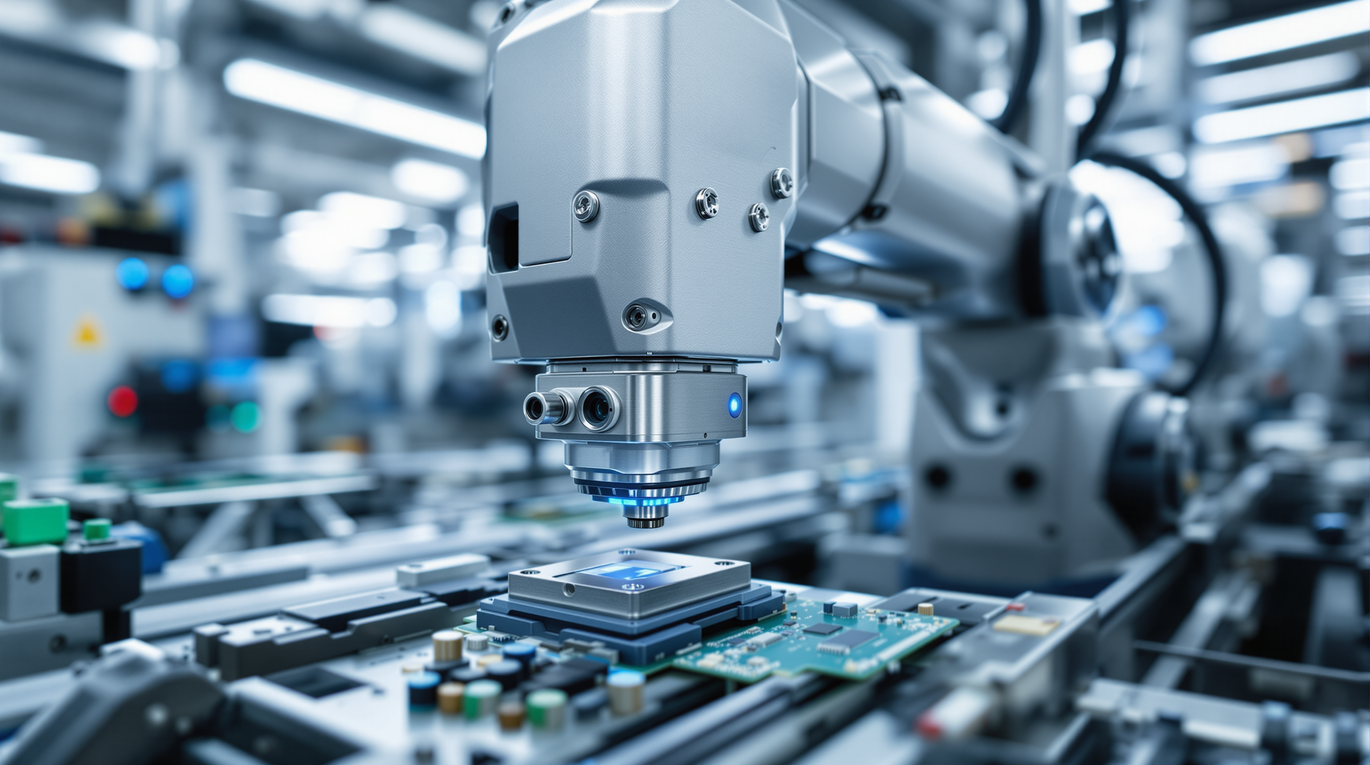
Smart sensors are revolutionizing manufacturing by reducing resource consumption by 30% to 50% in industrial applications. Our team has witnessed these advanced monitoring systems change how modern machinery operates. One electronics assembly plant reported its operational costs dropped 20% in just one year.
The industrial smart sensors market grows faster as manufacturers see their vital role in equipment health monitoring and process optimization. Our IoT sensor research shows these devices collect live data and adjust processes immediately to boost operational efficiency. Smart sensors and actuators help machine builders create more compact equipment that maintains high precision for multiple tasks.
This piece will show why smart sensors have become essential for modern compact machinery and how you can add them to your manufacturing processes effectively.
Understanding Smart Sensors in Modern Manufacturing
Modern manufacturing relies on a sophisticated network of smart sensors that combine sensing elements with advanced computing capabilities. These intelligent devices do more than simple measurement - they include microprocessors, storage, diagnostics, and connectivity tools that convert traditional feedback into useful digital insights.
Smart sensors act as machinery's eyes and ears and provide complete data about machine and production line status. Traditional sensors only give on/off status, while these advanced devices communicate diagnostic information and parameter data directly to controllers. They also excel at filtering out erroneous noise and deliver more accurate environmental data collection.
The smart sensor market will reach USD 143.65 billion by 2027, growing at a compound annual growth rate of 18.6%. The automotive segment leads with nearly one-fourth of the total market share and shows the highest growth potential through a CAGR of 21.7%.
- A base sensor to detect physical quantities
- An integrated microprocessor that analyzes data
- Dedicated memory to store measurements and operational parameters
- Built-in communication modules that connect to external devices
Smart sensors perform multiple critical functions effectively. They self-calibrate to adjust fabrication-related parameters and run self-diagnostics to detect internal signal errors. These devices measure various physical parameters simultaneously - from pressure and temperature to humidity and gas flow - which makes them a great way to get insights for modern manufacturing processes.
Smart sensors have brought substantial benefits to industrial applications. They enable live inventory tracking, optimize operational efficiency through automation, and lower maintenance costs through improved monitoring. Their power-up self-testing capability spots component failures immediately. The multi-sensing features allow them to measure temperature, flow, pressure, and density of a medium all at once.
Space-Saving Benefits for Compact Machinery
Smart sensors have become a defining trend in modern machinery design. Smart sensors now play a key role in creating compact yet powerful equipment. Manufacturers use advanced MEMS (Micro-Electro-Mechanical Systems) technology to reduce sensor sizes to submillimeter scales, which helps them combine components smoothly into space-constrained applications.
Recent sensor fabrication breakthroughs have created impressive space-saving benefits. MEMS technology has reduced the gas sensing area to less than 1/100th of the space needed by traditional printed sensors. These tiny components now fit effectively in tight spaces while delivering high performance.
Smart sensors prove especially valuable when space optimization matters in automated storage systems and compact machinery. These sensors enable precise compartment detection and reliable pallet positioning in high-bay warehouses despite space limitations. Compact distance sensors measuring just 0.99mm×2.5mm×3.2mm fit into small automatic shuttles in storage systems. They handle multiple tasks from checking shelf occupancy to collision avoidance.
Smart sensors have transformed power efficiency in compact designs. Modern MEMS-based sensors consume approximately 15mW of power, which shows a dramatic drop to 1/13th of conventional levels that needed 210mW. This improved energy efficiency allows battery-powered applications to run longer.
These advanced sensors offer superior functionality through:
- Integrated signal conditioning and processing capabilities
- Built-in self-diagnostic features
- Enhanced thermal response times of just tens of milliseconds
- Improved durability through finely tuned thermal stress calculations
The push toward smaller sizes continues to grow, especially in industrial applications where space comes at a premium. New sensors can now integrate directly into production lines while taking minimal space. These compact yet powerful devices maintain high precision in tasks of all types, from quality control to automated inspection processes.
Smart Sensors and Actuators Integration Guide
Smart sensors and actuators need proper setup and multiple factors to work at their best. Research shows that proper installation starts with strategic positioning. You must mount sensors securely in stable spots without blocking their data collection field.
Smart sensors work reliably only with a stable power supply that matches their voltage needs. Performance suffers when voltage suddenly changes. That's why backup power systems play a vital role in keeping operations running smoothly.
The right calibration makes a big difference in getting accurate readings. Smart sensors react very quickly to environmental changes. Wrong calibration leads to incorrect output values that end up affecting how well the whole system works.
Picking the right communication protocols is vital for smart sensor networks. The current options include:
- 38 protocols for process automation
- 19 protocols for building automation
- 12 protocols for automotive applications
Universal gateways help solve protocol compatibility issues by supporting common industry-specific protocols. This setup makes shared communication between different sensor types possible and keeps the system reliable.
Environmental protection remains a top priority during setup. Smart sensors need proper shields from high temperatures, pressure changes, humidity, and dust that can affect their readings. The right protective cases create strong barriers between sensors and harmful elements.
Data transmission capabilities need a thorough review during integration. The Mica2 platform, popular in industrial applications, handles data rates up to 38.4 K baud. Large-scale sensor networks might face transmission collisions that can cause random delays or lose data.
Security plays a key role in smart sensor integration. The setup should include:
- TLS encryption for gateway data delivery
- HTTPS protocols for app and API traffic
- Database AES encryption
- Two-step verification protocols
These security measures protect sensor data well and keep the system running smoothly throughout integration.
Conclusion
Smart sensors play a vital role in modern compact machinery and drive major improvements in manufacturing operations. These sensors cut resource usage by half and provide up-to-the-minute monitoring that benefits any industrial setup.
Manufacturing facilities that use smart sensors gain clear advantages. Equipment lasts longer and operational costs drop significantly. The sensors' advanced features make this possible through self-diagnosis, multi-parameter monitoring, and precise data collection. MEMS technology allows them to fit in small spaces.
Smart sensors need thoughtful integration planning to work well. The right positioning, stable power, proper calibration, and secure measures ensure they perform at their best. The market should reach USD 143.65 billion by 2027. Companies that want competitive edges through efficient, compact machinery designs will find these sensors increasingly important.